At Charles Day Steels, we recognise the importance of selecting the most appropriate metal cutting process for your metal fabrication project. With various cutting methods being more suitable to some industries and applications than others, it’s crucial to consider the right cutting process based on your unique requirements, industry, material and material thickness, as well as the intricacies and details necessary for your project.
With a series of cutting and profiling solutions provided at Charles Day, including Laser Cutting, Waterjet Cutting, Flame Cutting, Plasma Cutting, Profile Bending & Pressing, and much more, our experts are able to recommend the most appropriate metal fabrication process for your needs.
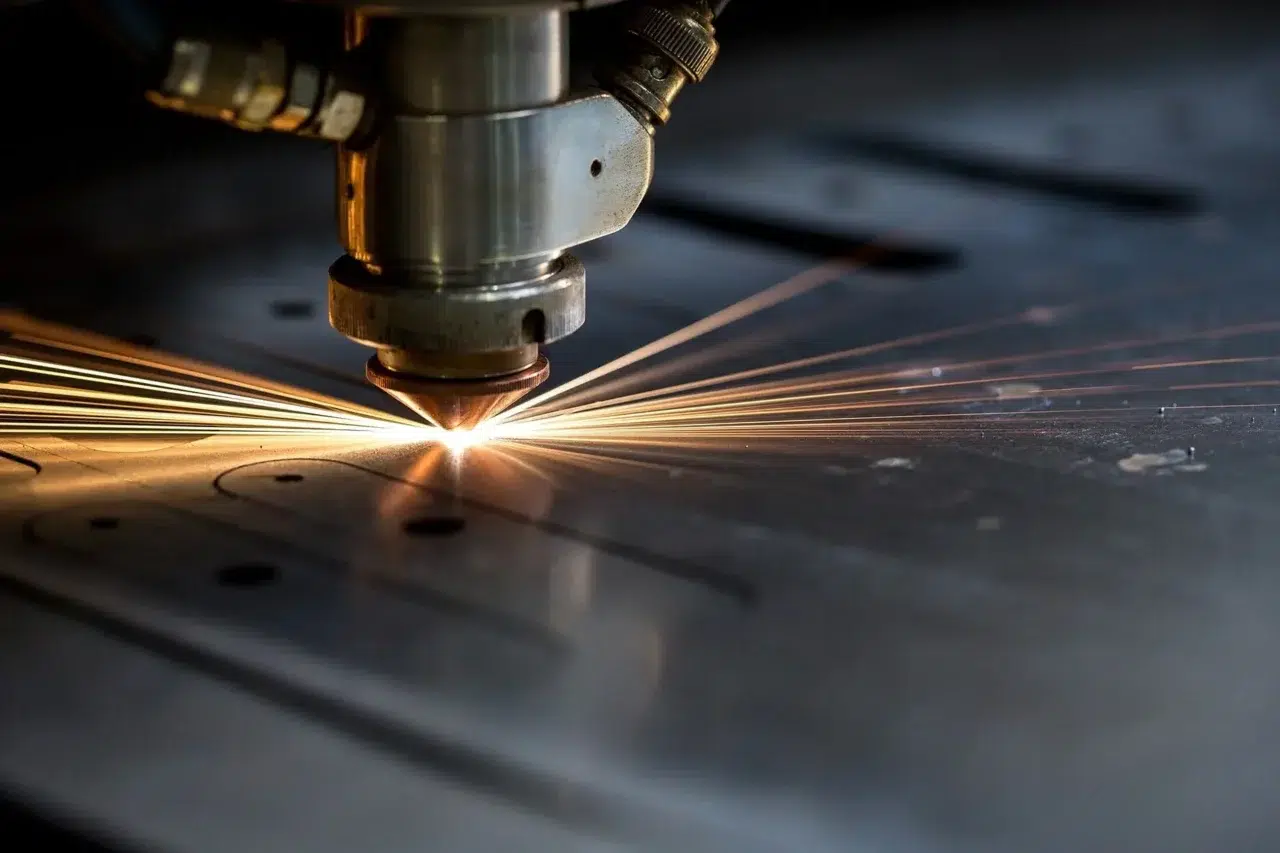
Laser Cutting
Laser cutting employs a powerful laser beam to melt, burn, or vaporise material, creating precise cuts; offering exceptional versatility, allowing for intricate designs and high-speed production. It is commonly used to cut thin sheets, tubes, and complex patterns.
Laser Cutting Applications & Industries
- Metal Fabrication
- Signage and Advertising
- Prototyping and Rapid Manufacturing
- Electronics and PCB Manufacturing
- Automotive Industry
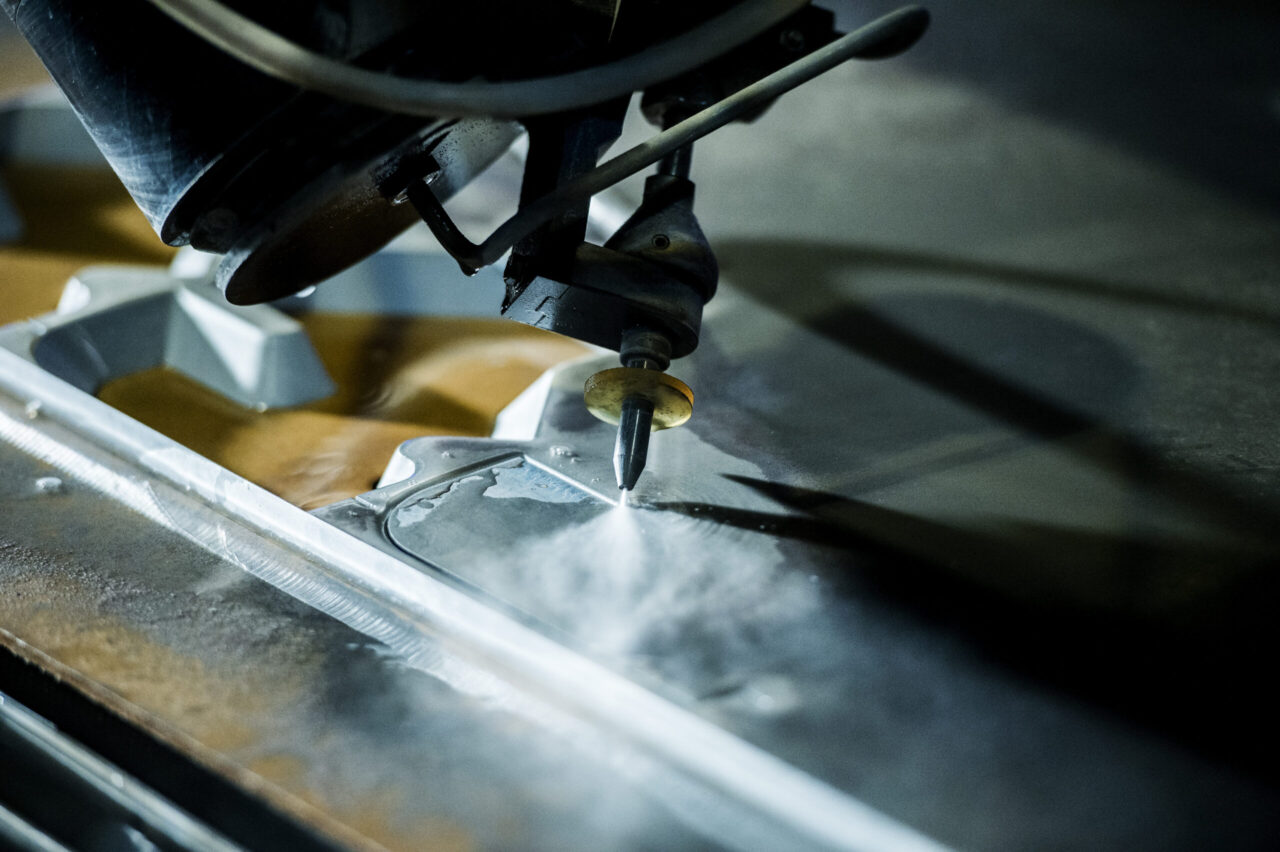
Waterjet Cutting
Waterjet cutting utilises a high-pressure jet of water mixed with abrasive particles to cut through metal materials. This process is highly versatile and can handle a wide range of materials; providing excellent precision, whilst avoiding heat-affected zones or material distortion, making it suitable for delicate or heat-sensitive materials.
Waterjet Cutting Applications & Industries
- Architecture and Interior Design
- Automotive Industry
- Food Industry
- Manufacturing and Fabrication
- Packing and Display
- Artistic and Decorative Applications
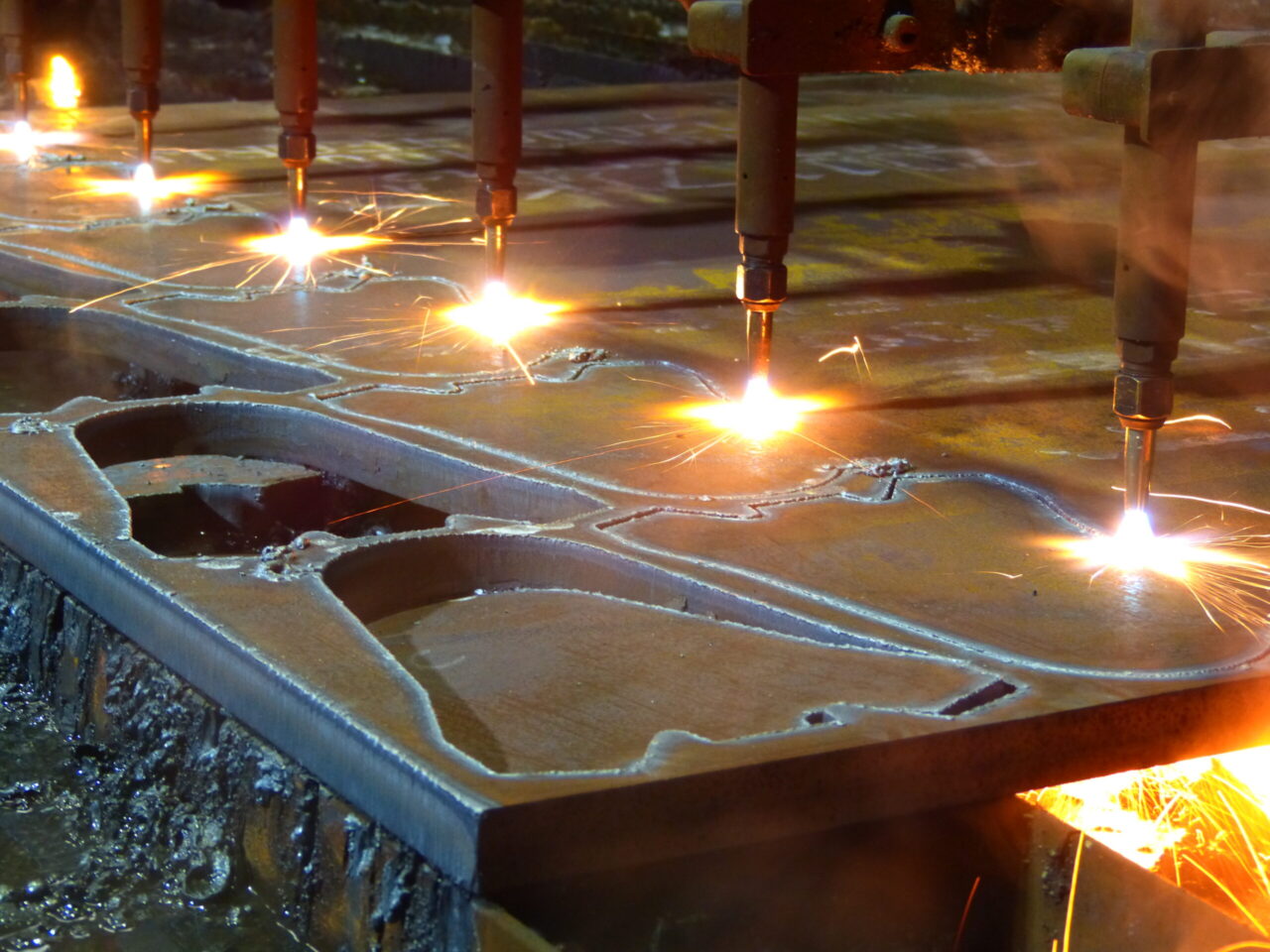
Flame Cutting
Flame cutting employs the heat generated by a high-temperature flame to melt and remove material from a cut. While it may not offer the same precision as some other cutting methods, flame cutting is valued for its versatility, cost-effectiveness, and ability to handle thick materials.
Flame Cutting Applications & Industries
- Structural Steel Fabrication
- Shipbuilding and Offshore Industry
- Heavy Equipment Manufacturing
- Oil and Gas Industry
- Scrap Metal Recycling
- Agricultural and Farm Equipment
- Artistic and Decorative Applications
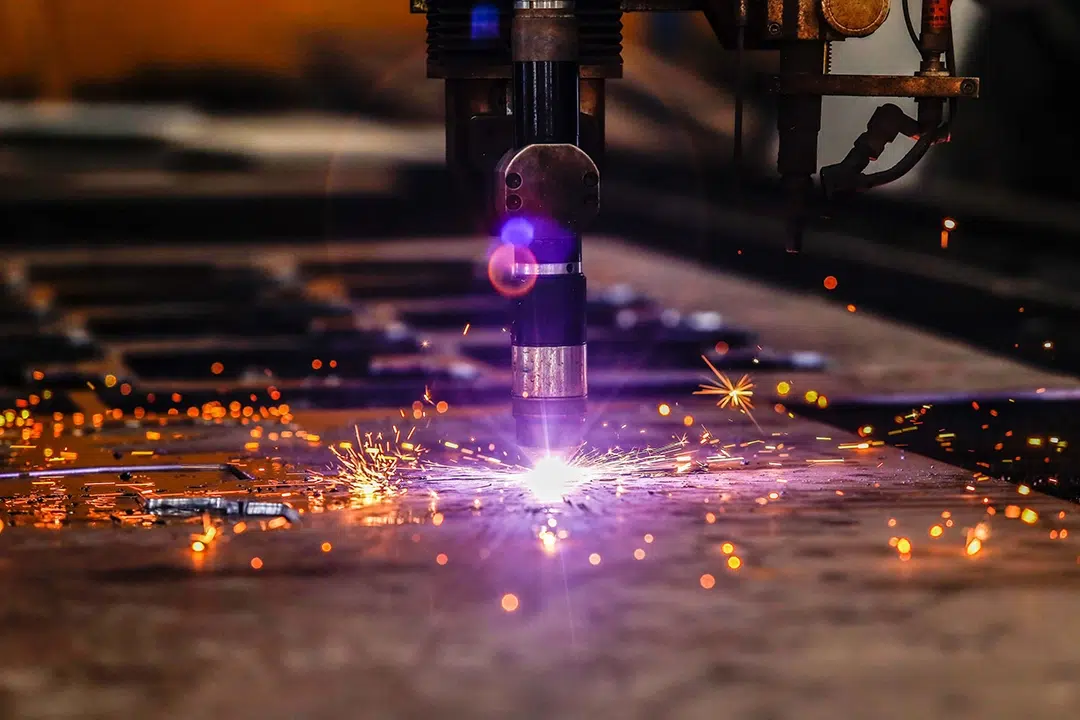
Plasma Cutting
Plasma cutting utilises a high-velocity jet of ionised gas to melt and remove material. With its ability to cut through a wide range of conductive materials, plasma cutting has become a popular choice in various industries.
Plasma Cutting Applications & Industries
- Metal Fabrication and Manufacturing
- Automotive and Transportation
- Construction and Infrastructure
- HVAC and Ductwork
- Art and Sculpture
- Shipbuilding and Marine Industry
- Aerospace and Aviation
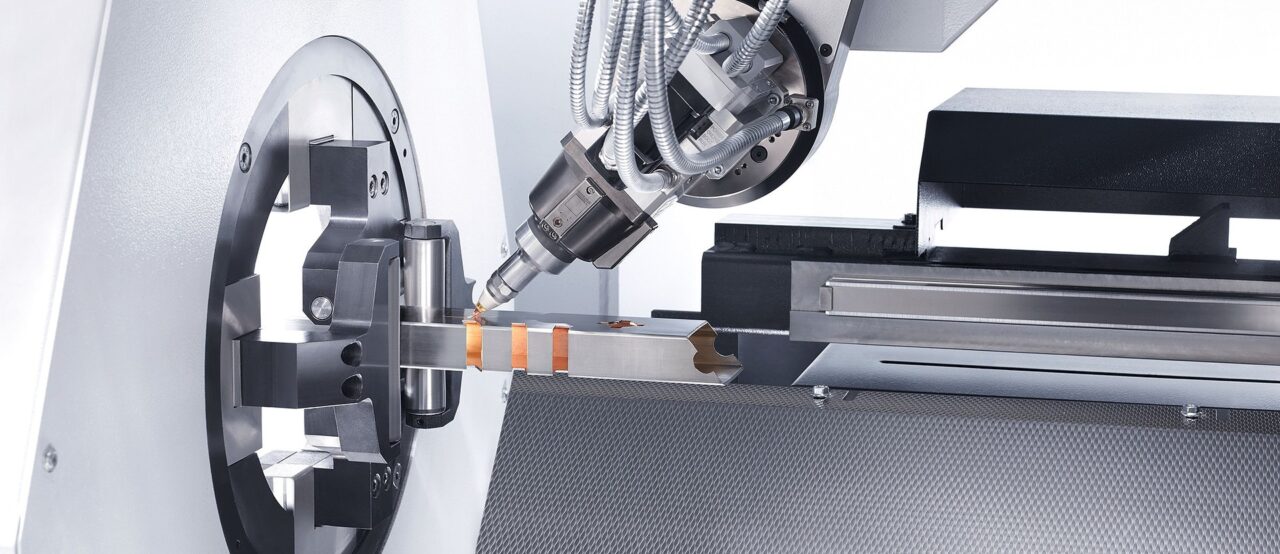
Tube Cutting
Tube cutting is a specialised metal cutting process that involves the precise cutting of tubes and pipes to specific lengths or shapes. This technique is widely used in various industries that rely on tubular components for their manufacturing processes.
Tube Cutting Applications & Industries
- Automotive and Transportation
- Plumbing and HVAC
- Construction and Infrastructure
- Furniture Manufacturing
- Aerospace and Defense
- Medical and Pharmaceutical Industries
- Renewable Energy Sector
How Do I Select the Correct Metal Cutting Technique For My Metal Fabrication Project?
Selecting the correct metal fabrication process for your metal fabrication project is crucial to achieving your desired results. Some key considerations include:
Material Type and Thickness:
Different cutting techniques are suitable for specific materials and thicknesses. For example, Laser Cutting is excellent for thin metals, while Waterjet Cutting is versatile and can handle a wide range of materials and thicknesses.
Precision and Tolerance Requirements:
Evaluate the precision and tolerance requirements of your project. Laser cutting and Waterjet cutting are known for their high precision, while other techniques like Plasma Cutting may have slightly lower tolerances.
Cutting Speed:
Some techniques, such as plasma cutting, offer high cutting speeds, making them suitable for large-scale production. Laser cutting and waterjet cutting can also achieve relatively high speeds, depending on the material and thickness being cut.
Complexity of Shapes and Designs:
If your project involves intricate shapes or complex designs, techniques like laser cutting and waterjet cutting offer excellent capabilities; achieving precise cuts and intricate patterns with ease, allowing for greater design flexibility.
Heat Sensitivity:
Evaluate whether your material is sensitive to heat. Techniques like laser cutting and waterjet cutting produce minimal heat-affected zones, making them ideal for heat-sensitive materials, whereas plasma cutting generates significant heat, which may affect certain materials.
Cost Considerations:
Different cutting techniques vary in terms of equipment costs, maintenance requirements, and operational expenses. Evaluate the overall cost-effectiveness of each technique based on your project’s specific requirements.
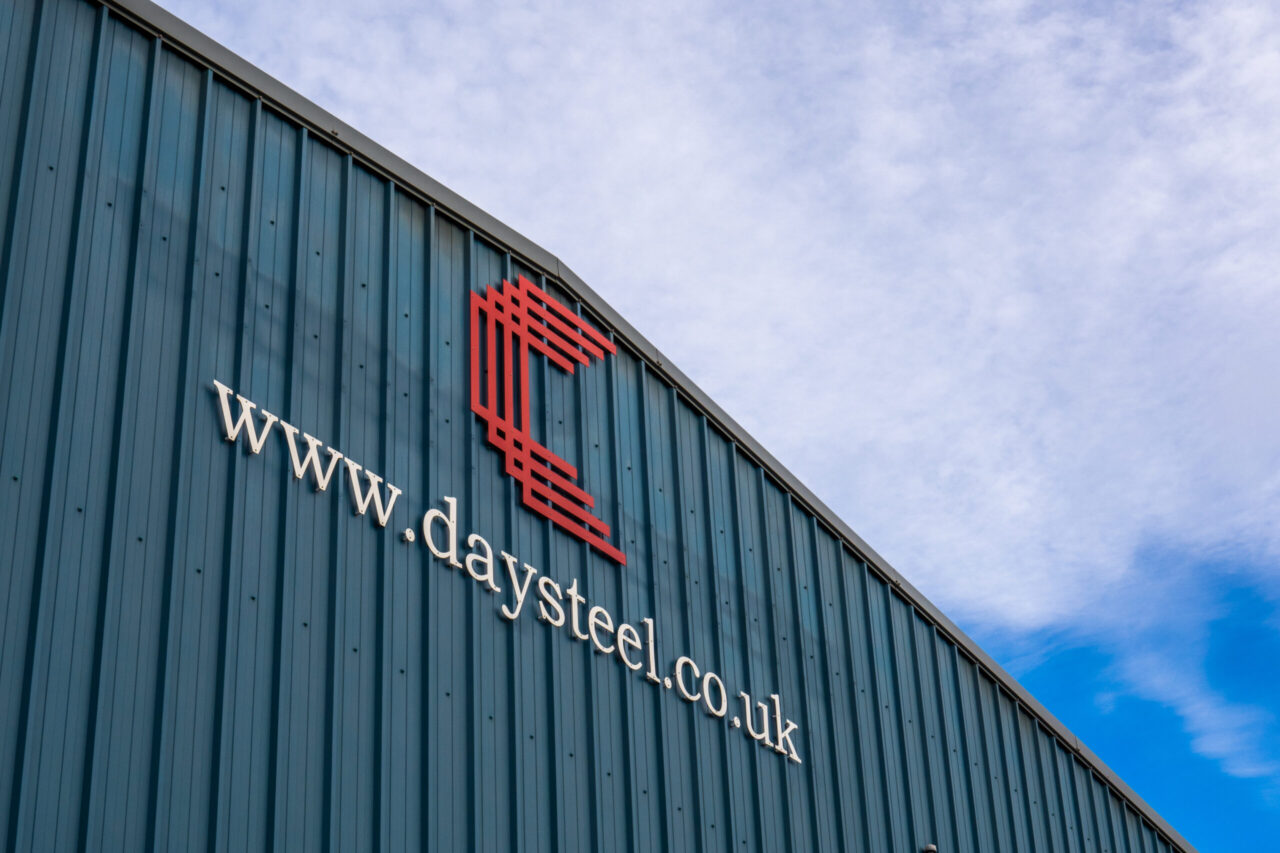
Get in Touch with the experts
For more guidance and assistance, contact Charles Day Steels.