50 Degree
Bevel cutting Angle
6510mm x 2600mm
Max Straight Cutting
Up to 40mm
Cutting thickness
Efficient & Cost Effective
Machining alternative
Complex
Bevel Geometries
Achieve Revolutionary Precision and Efficiency with Our Laser Bevel Cutting Services
At Charles Day Steels, we are excited to offer advanced laser bevel cutting services, delivering unmatched precision and efficiency to meet all your bevel cutting needs. Our latest investment in cutting-edge laser bevel technology, allows us to provide unparalleled quality and performance, setting a new benchmark in the metal profiling industry.
Bevel Types
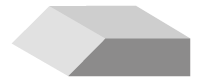
Top Bevel
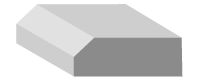
Top Bevel
with a land
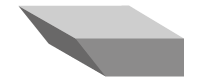
Bottom Bevel
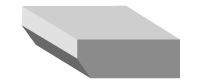
Bottom Bevel
with a land
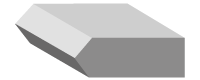
X Bevel
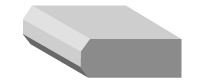
K Bevel
Key Benefits
Versatile Cutting Angles
Capable of cutting at any angle up to 50 degrees on various materials.
High Power and Precision
Our laser cutting technology ensures precise cuts on materials up to 40mm thick.
Large Cutting Bed
Bevel cutting on sheet sizes up to 6125mm x 2030mm.
Straight cutting on sheet sizes up to 6510mm x 2600mm.
Fabrication Ready, Weld Prepped and Bevelled Parts
Creates flawless chamfers or bevels.
Tolerance
Profiling tolerance
/-0.12mm to +/-0.75mm
Material Thickness vs Bevel Angle
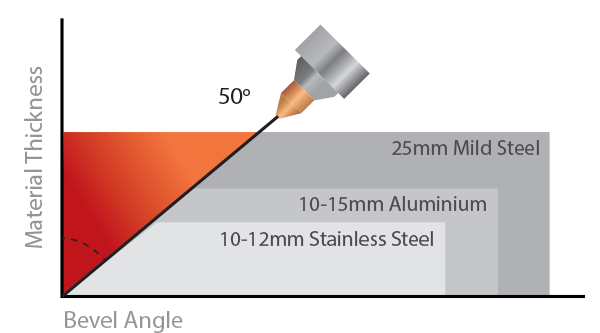
Cut quality and tolerance can depend on material thickness, for optimum cut quality please discuss with our sales team.
Bed Sizes
6510mm x 2600mm
Straight Cutting
6125mm x 2030mm
Bevel Cutting
Why Laser Bevel Cutting?
Laser bevel cutting is an incredibly efficient and cost-effective process, ideal for high-capacity production on short lead times. It offers precise cuts with an accuracy of ±0.25mm and requires no grinding after cutting, making it a time-effective alternative to traditional methods.
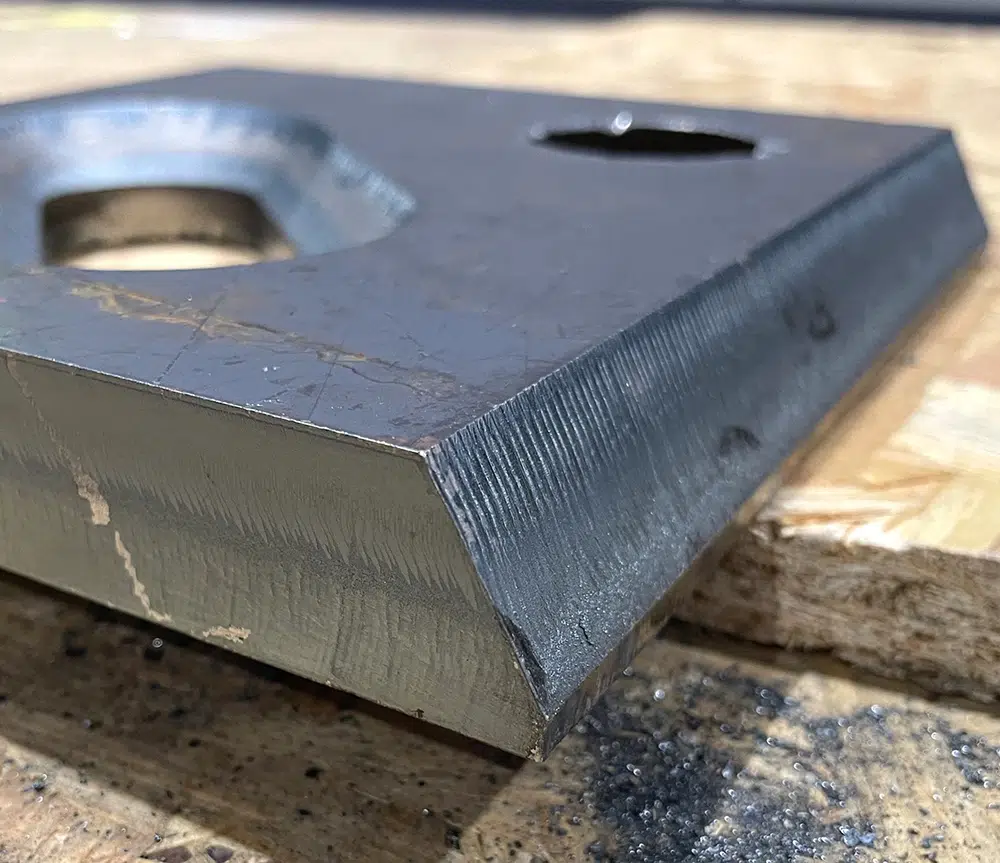
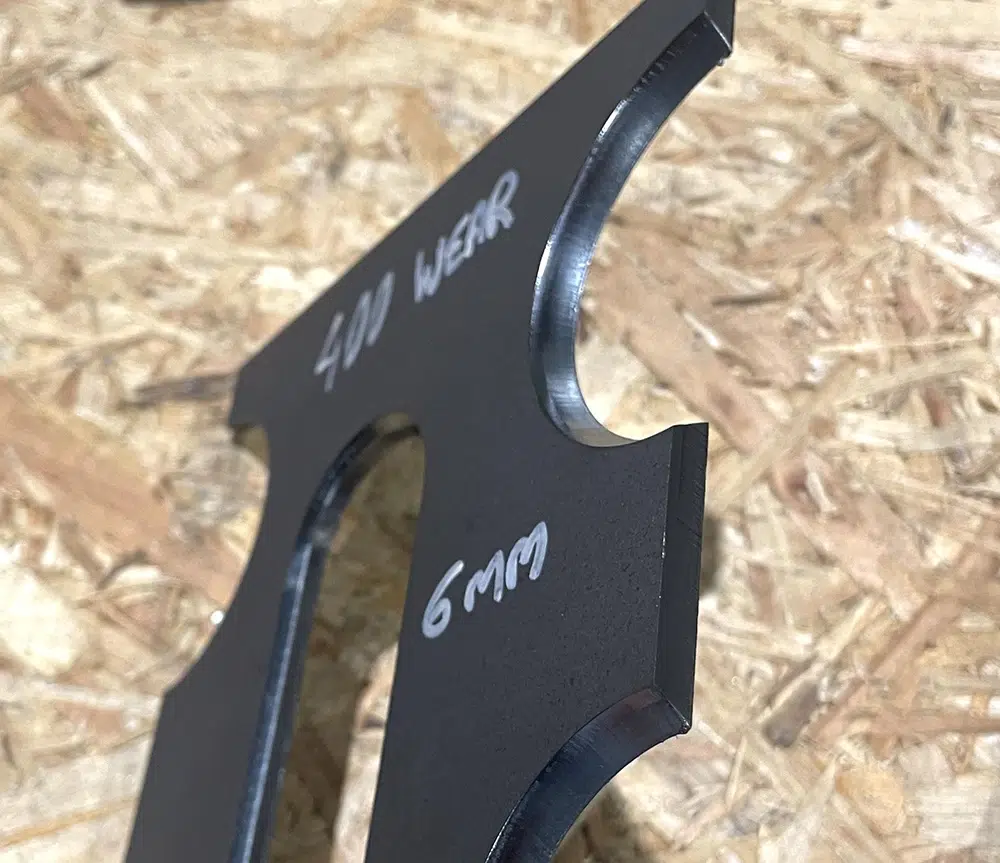
The Power of Laser Bevel Cutting
Our laser bevel cutting services are designed to handle the most complex cuts with remarkable ease and precision, offering several advantages:
Versatile Cutting Angles
Capable of cutting at any angle up to 50 degrees on various materials including mild steel, alloy, and stainless steel. This flexibility eliminates the need for manual grinding and weld preparation, streamlining your fabrication process and saving you valuable time.
High Power and Precision
Our laser cutting technology ensures precise cuts on materials up to 40mm thick, maintaining exceptional accuracy and quality.
Large Cutting Bed
The spacious cutting bed allows for rapid processing of large bevel parts, including 6510mm x 2600mm for straight cutting and 6125mm x 2030mm for bevel cutting; significantly reducing production times and costs.
Benefits of Our Laser Bevel Cutting Services
Choosing Charles Day Steels for your laser bevel cutting needs comes with numerous advantages:
Seamless Transition to Assembly
Our laser bevel cutting technology minimises post-processing time and labour costs, providing you with fabrication-ready parts in one seamless process.
Exceptional Lead Times
Operating 24/7, we ensure quick turnaround times without compromising on quality, even for large-volume and high-complexity projects.
Unmatched Accuracy
Our fully automated process guarantees zero margins for error, delivering precise and consistent cuts every time.
Cost-Effective Solutions
By eliminating the need for additional weld preparation, we offer cost-efficient bevel procurement, passing the savings on to our customers
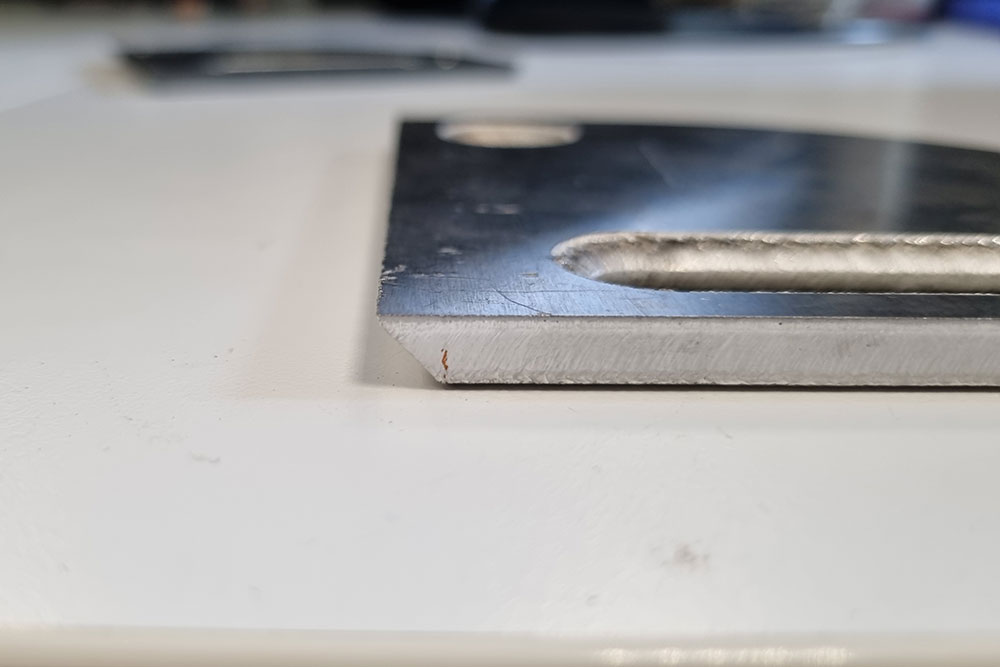
Waterjet Bevel vs. Laser Bevel Cutting
We also offer waterjet bevel cutting services, allowing us to cater to a wider range of needs and materials. Here’s how the two methods compare:
Laser Bevel Cutting:
- Efficient and cost-effective
- Precise to ±0.25mm
- Ideal for high-capacity production
- Quick turnaround times
- No grinding required post-cutting
Waterjet Bevel Cutting:
- Ideal for thicker materials (up to 270mm)
- Cold cutting process suitable for heat-sensitive applications
- Accurate to ±0.25mm
- Supports multi-head cutting for higher productivity
Get in Touch
Experience the future of laser bevel cutting with Charles Day Steels. Contact us today for a free quote and discover how our advanced laser bevel cutting services can enhance your next project.
For more information about our Laser Bevel Cutting services and to discuss your project requirements, click here to get in touch.
Laser Bevel Cutting FAQs
What is laser bevel cutting?
Laser bevel cutting is a precise manufacturing process that uses a laser to cut materials at an angle, creating bevelled edges. This technique is commonly used in industries such as automotive, aerospace, and metalworking to produce parts with angled edges for better fit and assembly.
What materials can be cut using laser bevel cutting?
Laser bevel cutting can be used on a variety of materials including metals (such as steel, aluminium, and titanium), plastics, wood, and composites. The choice of material depends on the specific requirements of the project and the capabilities of the laser cutting machine.
How does laser bevel cutting work?
The process involves directing a high-powered laser beam at the material to be cut. The laser melts, burns, or vaporises the material along the cutting path, creating a bevelled edge. The angle of the bevel can be adjusted by tilting the laser head or by using a specialised cutting head.
What applications use laser bevel cutting?
Laser bevel cutting is used in various applications including:
- Sheet Metal Fabrication: Creating parts with bevelled edges for better welding and assembly.
- Aerospace: Cutting components that require precise angles for aerodynamics and assembly.
- Automotive: Manufacturing parts with angled edges for improved fit and strength.
- Signage: Producing signs with bevelled edges for aesthetic appeal.
How does laser bevel cutting compare to traditional bevel cutting methods?
Laser bevel cutting offers several advantages over traditional methods such as plasma or mechanical cutting:
- Higher Precision: Laser cutting produces more accurate and cleaner edges.
- Minimal Heat Affected Zone (HAZ): The laser’s focused heat reduces the area affected by heat, preserving the material properties.
- Reduced Waste: The precision of laser cutting minimises material waste.