Metal cutting plays a vital role across various manufacturing sectors to facilitate the unique requirements of several industries. With its diverse capabilities, the steel industry significantly contributes to the UK economy, with an annual output valued at approximately £2.4 billion. The process of metal cutting can be complex and encompasses many variants of methods which are detailed throughout this comprehensive guide.
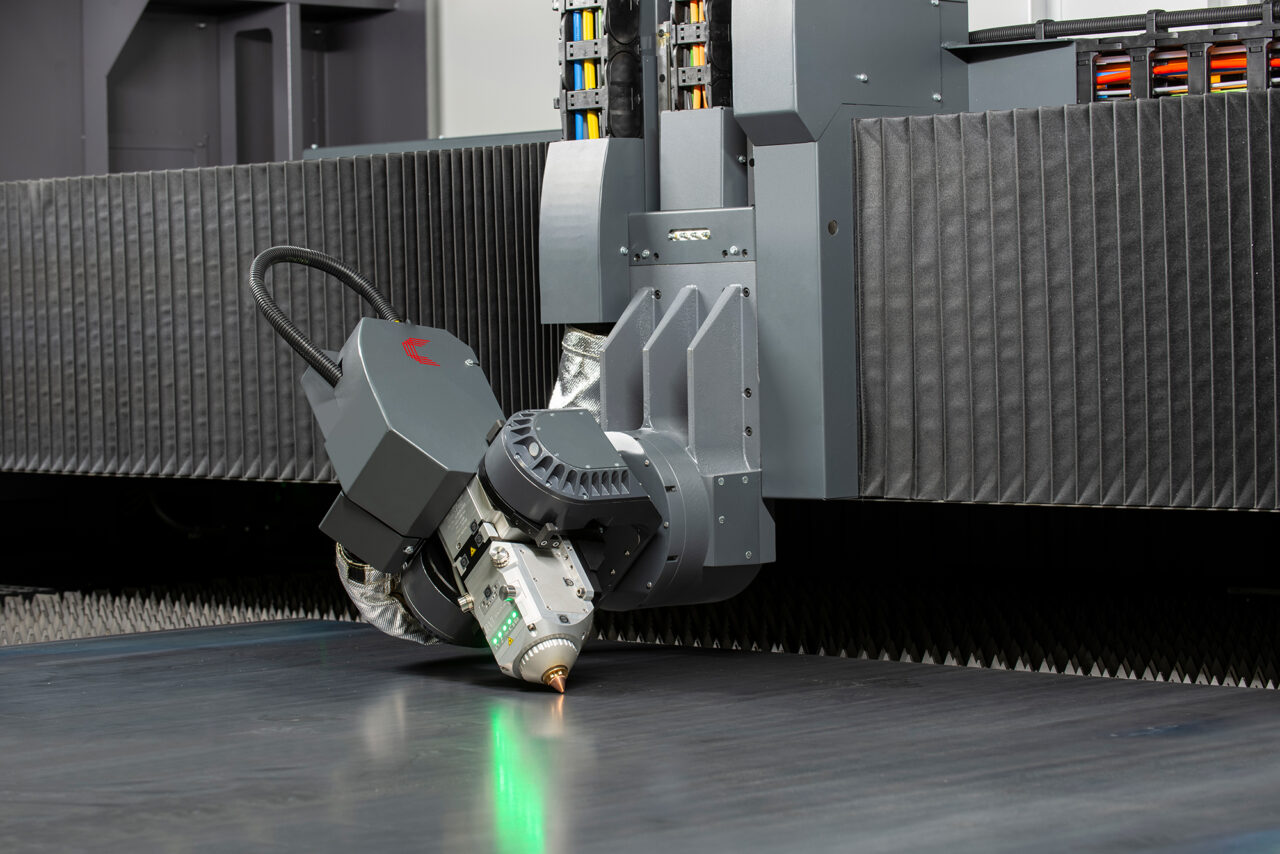
Metal Cutting Applications
Metal cutting is utilised across a broad spectrum of industries due to the remarkable versatility of its applications. The most common industries include:
Automotive: Car panels, interiors, intricate components.
Aerospace: Panelling and intricate parts.
Medical: Medical devices and surgical instruments.
Electronics: Electronic components and circuit boards.
Textiles and Jewellery: Various upholstery, clothing and jewellery designs.
Prototypes: New designs, products, and test designs.
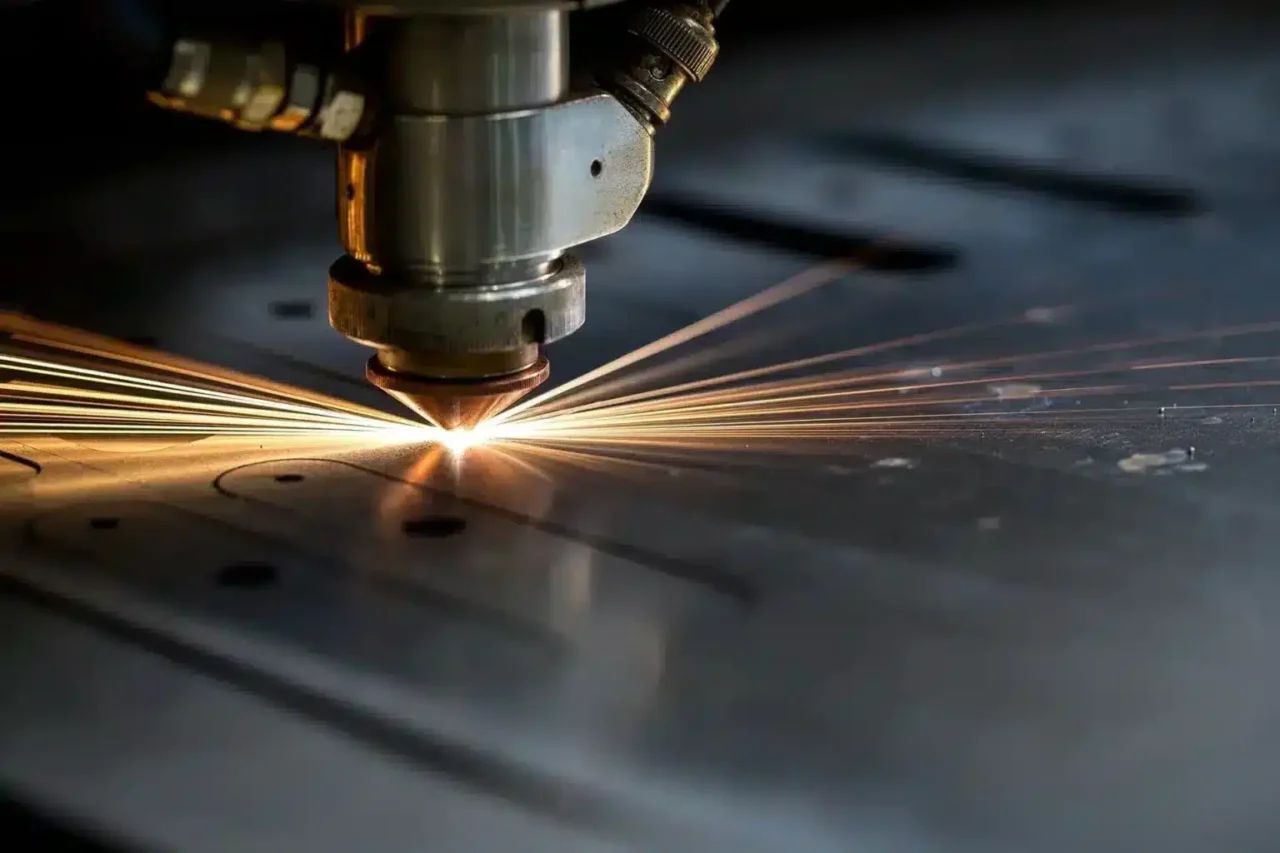
The Processes of Metal Cutting
The fundamentals behind metal cutting can be defined by its various processes, each with its own purpose, capabilities and desired output for project requirements.
Mechanical Cutting
Mechanical cutting is a process that utilises tools and manual exertion to remove material from metals. This technique operates differently from thermal applications and is capable of producing highly precise components by applying physical force to manipulate metal types. Common methods of mechanical cutting include:
Shearing: Utilising a sharp edge, typically with shears, the metal is severed and is common when cutting straight lines.
Punching: A punch and die machine creates holes in a metal sheet to achieve a desired pattern, shape or slot. If the machine is strong enough, it will be able to handle a greater metal depth.
Drilling and Tapping: A drill will exert a rotating downward force to create holes within the metal, while the tapping process creates internal threads to accommodate screws or bolts.
Bending and Pressing: Large machines can exert additional force to shape metal from a flat surface into dimensional shapes, adhering to specified angle parameters.
Deburring: This is performed at the end of fabrication to remove excess metal that has left sharp edges or unwanted blemishes as part of the processing.
Cold-Cutting
This method generates force through non-contact cold processes, eliminating the need for heat, or tools that utilise mechanical force.
Waterjet Cutting: Waterjet cutting is a technique that uses a high-pressure jet of water, which is often combined with abrasive materials such as sand, to effectively cut through metal of various thicknesses while producing bevelled edges across a range of tolerances. This process is preferable to combat concerns of material distortion, particularly against heat-sensitive or delicate materials.
Thermal Cutting
A popular metal cutting technique, this method employs a high heat energy source to melt and vaporise the metal, thereby establishing separation and precise cuts within rapid lead times.
Flame Cutting: A high-temperature flame is used to melt and remove material from metal, offering the ability to process thicker materials while providing a cost-effective solution to metal cutting.
Plasma Cutting: A high-velocity jet of ionised gas effectively melts and removes material from electronically conductive metals. This process is highly versatile and produces minimal distortion during processing.
Laser Cutting: A powerful laser beam vaporises metal to create highly precise cuts that are dynamic and non-contact, allowing for the fabrication of complex designs in expedited lead times.
Additional Processes
Tube cutting utilises various fabrication methods in order to shape tubes and create structural shapes or channels across various dimensions and designs. This type of metal cutting is utilised most in industries that require tubular components.
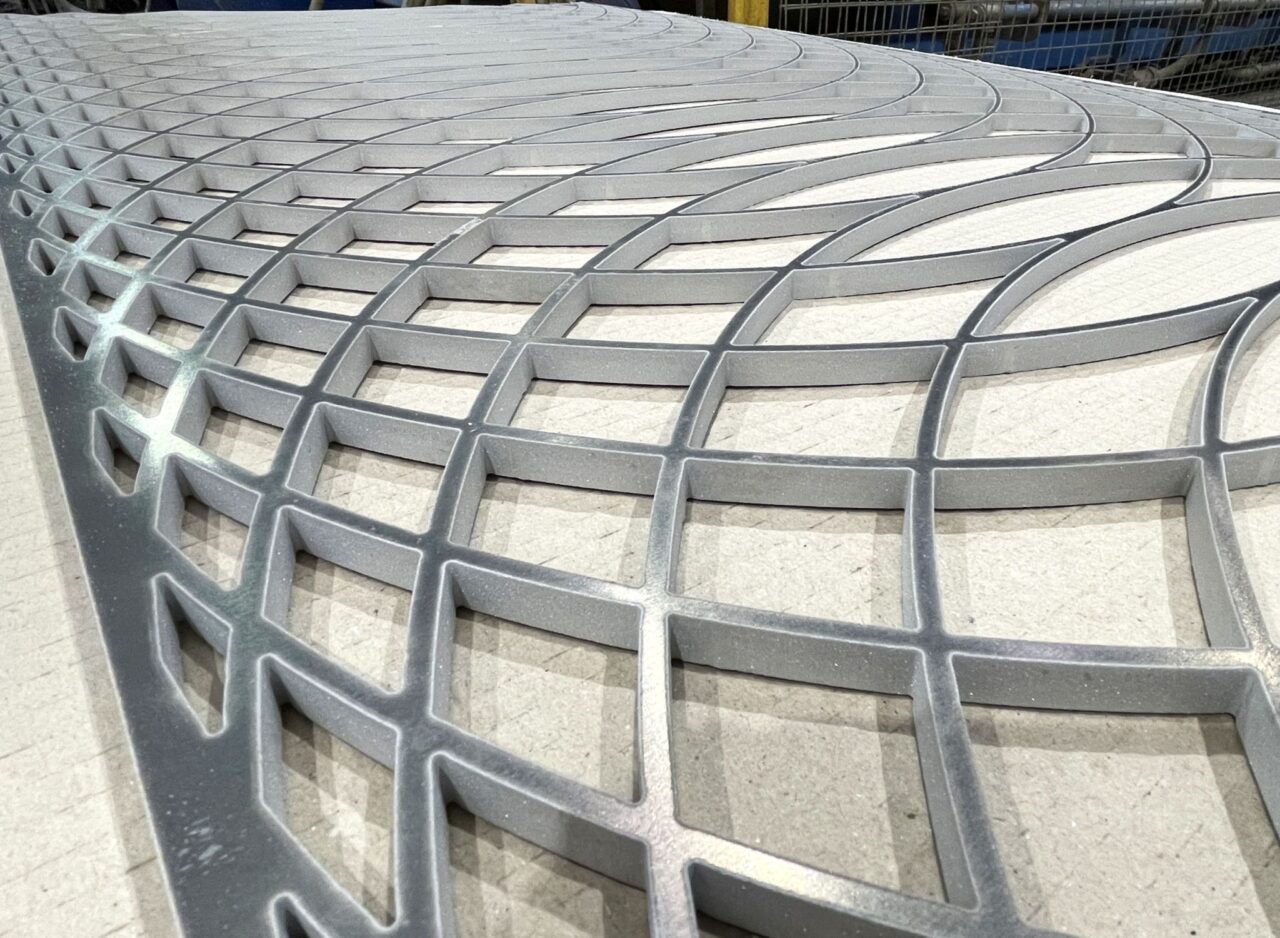
What Can Affect Metal Cutting?
There are several factors to consider when deciding which metal is suitable for your project, these fall into three main categories:
Metal Properties: There are a plethora of metal behaviours that can dictate which one is the best fit for a project’s individual requirements. This can include metal hardness, brittleness, ductility and heat resistance, which can all have an impact on the finished product.
Project Complexity: Designs that require a high degree of difficulty and intricate executions should consider a cutting type that will provide the highest level of finish, rather than focusing on speed. Achieving a high-calibre product is beneficial for project timelines and diminishes waste, retaining revenue throughout the timeline.
Cutting Method: The cutting process is subjective to the specified project and metal requirements; a quality fabrication company can provide insight into the most appropriate method. For example, despite its reduced lead time, waterjet cutting would be the optimal choice for handling thick or heat-sensitive materials due to its cold processing and clean execution.
Common Materials in Metal Cutting
Metal cutting is a versatile process that can handle various metals up to a specified thickness. Each method will have its own tolerances, generally for laser cutting, the depth is as follows:
- Stainless Steel: 50mm thickness
- Mild/Carbon Steels: 50mm thickness
- Aluminium: 40mm thickness
- Nickel Alloys: 25mm thickness
- Copper: 20mm thickness
- Brass: 20mm thickness
- Bronze: 20mm thickness
- Titanium: 10mm thickness
Fabrication is not always limited to metal sheets, with the additional capacity to process varying materials including acrylic, textiles, glass, wood, and paper.
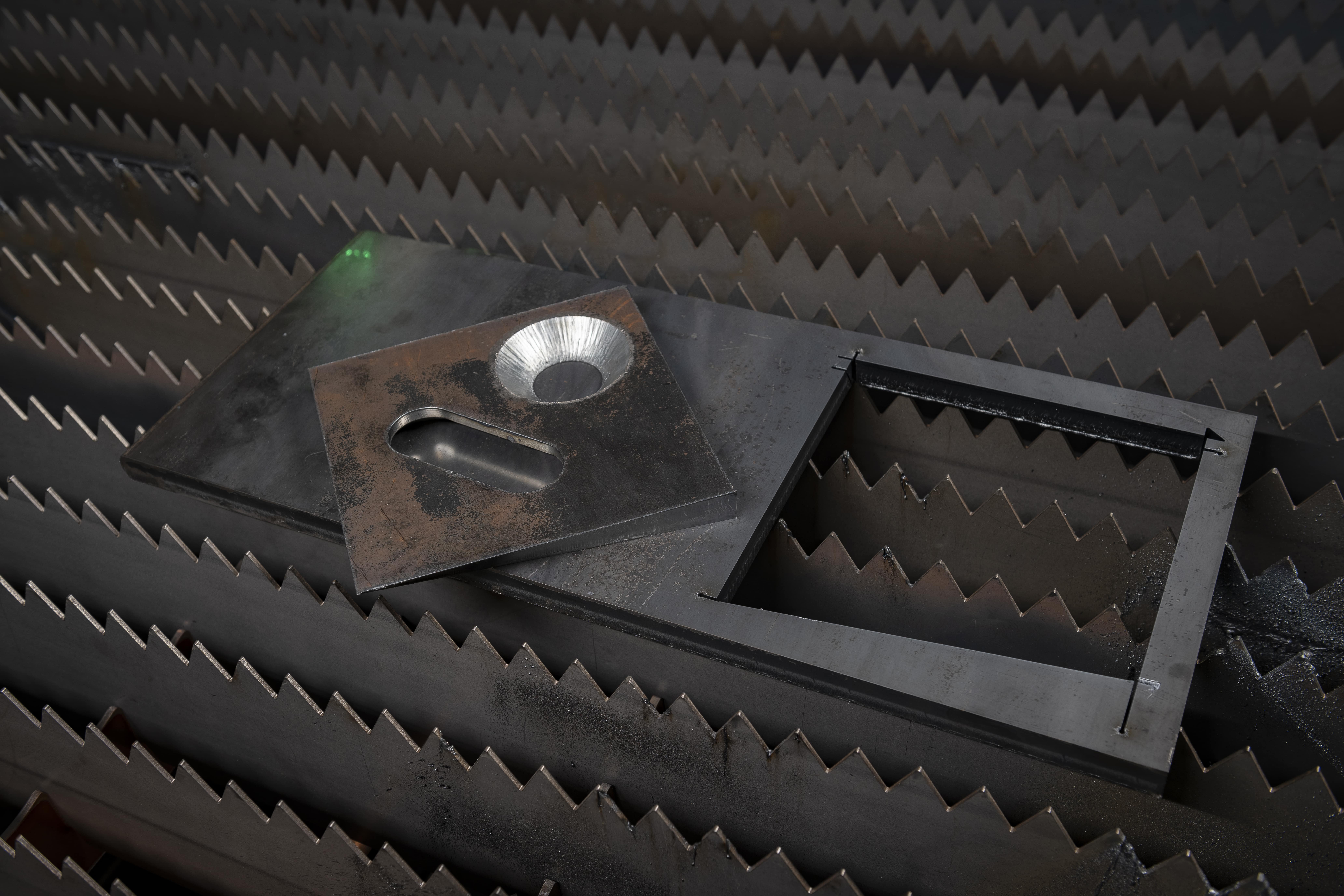
Experience Exceptional Metal Profiling with Charles Day Steels
Charles Day Steels provides high-quality mechanical, waterjet, flame, plasma, and laser cutting solutions for all projects regardless of complexity and scale. Based in the heart of Sheffield, we process a broad range of materials, with the ability to source materials within 24 to 48 hours if not available in our extensive inventory.
Our expansive portfolio of cutting and profiling services is reflected in our four decades within the steel fabrication industry, ensuring we continuously invest in the latest innovative technology for the benefit of our clients.
If you seek quality metal profiling and outstanding service, reach out to our team of experts today to discuss your project needs and receive a free no-obligation quote.