Waterjet cutting brings the accuracy and repeatability of computer control together with the power of high pressure pump technology. Advances in materials, control and pump technology have aided the development of high pressure waterjet machines capable of achieving powerful cutting. What was once a crude cutting method is now a precision tool used in the supply of parts to the aerospace and nuclear industries.
To meet structural integrity standards for critical components, suppliers to the aerospace industry often use CNC waterjet to cut net shape parts. As a cold cutting technology, waterjet does not affect the base part material, unlike laser cutting, which can cause structural damage. Known as a heat affected zone, or HAZ, overheating can compromise integrity, a key example being specialist alloys used within aerospace manufacturing which can suffer heat-related microcracks.
The Right Finish
CNC waterjet is considered a cutting technology but in practice, it is a computer guided, precise erosion process. This versatile profiling technology is able to €˜cut’ almost any material, including metal, plastic, and stone, within a +/- 0.25mm tolerance.
Waterjet cutting finish, how smooth or rough the cut edges are, varies depending on material depth and hardness, and how fast it is cut. Fast cutting lowers production costs but sacrifices edge quality, whereas slow cutting has a higher cost per part but achieves a fine finish. The machine operative will use pressure, speed, and abrasives, where required, to attain the right finish for the job.
Separation Cut
Maximum cutting speed, or feed rate, delivers a rough cut with course grooves and some nicks in the material. This cutting speed is ideal for high volume orders with few corners and radii. Separation cut delivers a low cost per part where edge quality is not a priority.
Medium Cut
The standard waterjet cutting speed where edge quality reaches a median point between rough and fine. Edge quality is rough, but grooves are less course and materials do not nick. A medium output speed with a good balance of quality and cost per part. Able to cut corners and radii with visible grooves.
Fine Cut
Ideal for cutting complex designs, thick and hard materials, and achieving maximum edge quality. Slow cutting does incur a higher processing cost per part but delivers optimum finish. Fine cut can deliver downstream efficiencies for some projects which outweighs the higher profiling cost.
Added Abrasive
Waterjet cutting power can be augmented with the addition of an abrasive agent. Depending on the material being cut, operatives add a hard, fine grain abrasive such as garnet to generate the maximum cutting force. An abrasive agent is usually added to waterjet cutting for the hardest materials with softer materials cut using pure water. Added abrasive is most commonly used to cut steel, aluminum, stone, ceramic, and thick plastics. Softer, or more delicate materials such as rubber, thin plastics, foam, fabric, and even food products require only pure water cutting power.
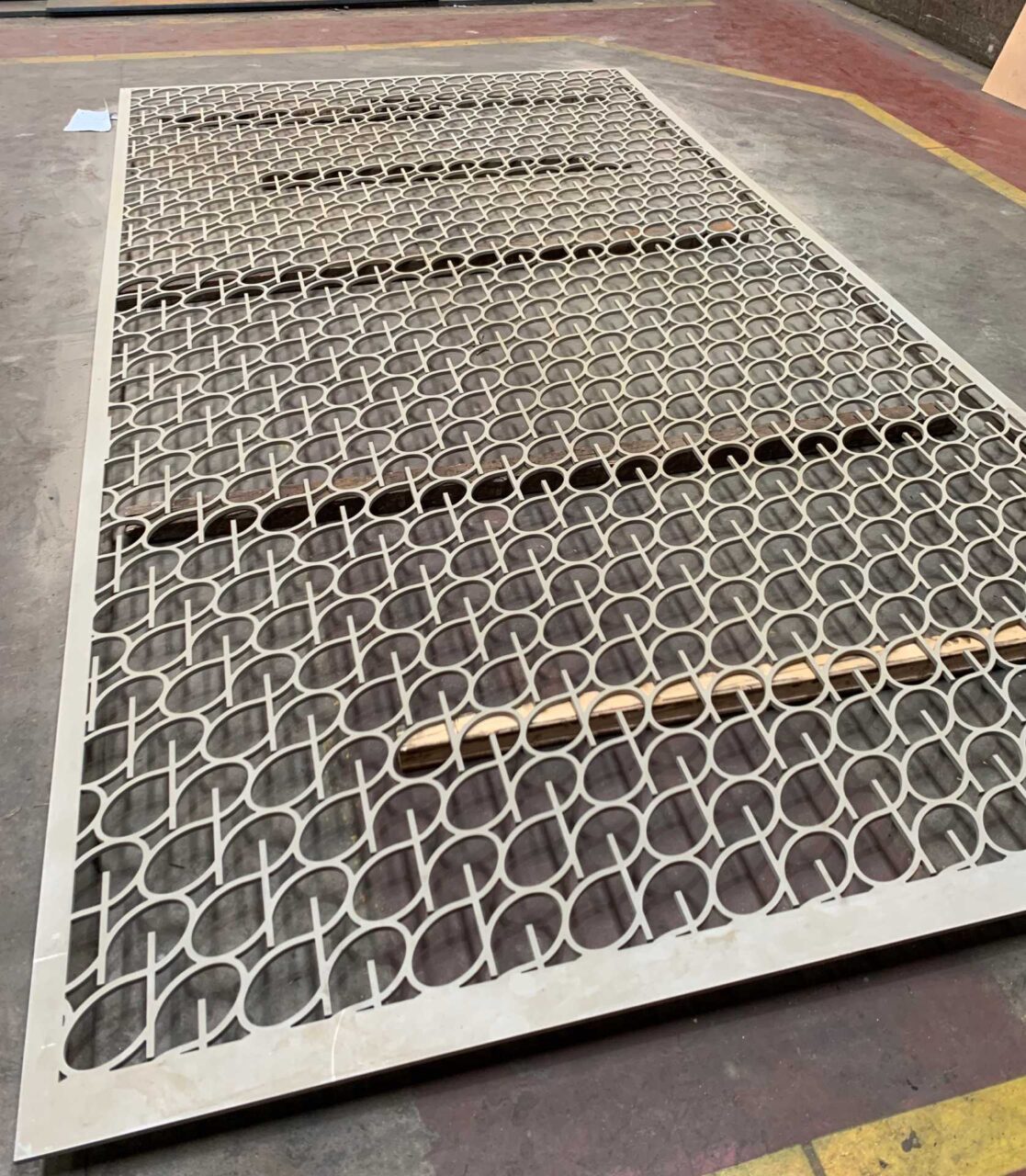
Downstream Efficiencies
Fine cut in waterjet tends to be used to meet aesthetic or efficiency project objectives. Cutting projects, such as the production of premium balustrading, benefit from the slower throughput rate of fine cut to ensure edges require no additional profiling to achieve a smooth, aesthetically pleasing finish.
In other cases, such as structural steel cutting for construction projects, benefit from a medium or fine cut to reduce downstream weld preparation. The lower throughput rate and higher cost per part can be offset by downstream process savings.
Charles Day Waterjet Cutting Service
A 24-hour waterjet cutting using a suite of three high-pressure multiheaded machines, capable of cutting highly complex profiles, fast. Cutting beds measuring up to 9m x 4m profile largescale projects to an accuracy of +/-0.25mm and edge squareness of 1 ° draft angle through the material.
Continuous investment in water pump power and large cutting beds puts Charles Day at the forefront of outsourced waterjet cutting:
- Bed size – 9m x 4m
- Hard material max. cutting depth – 230mm
- Cutting jets – 3 per machine – rapid throughput for fast turnaround
- Kerf/cut width – 1.0mm
- Tolerance – +/-0.25mm.
Send over a drawing to see how CNC Waterjet edge quality can make the right cut in your next project, with a no-obligation quote.