Here at Charles Day Steels, our many years of experience and expertise mean that we understand more than most the importance of selecting the correct metal profiling service to meet your project’s requirements.
While flame cutting and plasma cutting both offer their unique advantages and applications, understanding the nuances between these two methods is essential for making informed decisions on steel processing. We specialise in many profiling techniques, including flame cutting and laser cutting, which we believe offer superior benefits across various applications.

What is Flame Cutting?
Flame cutting, also known as oxy-acetylene cutting, is a tried-and-true method for profiling steel. This technique leverages the chemical reaction between oxygen and a fuel gas (typically acetylene) to produce a high-temperature flame capable of cutting through thick steel. With over 45 years of experience, Charles Day Steels has perfected this process to deliver efficient and cost-effective results.
Key Features of Flame Cutting
Thickness Capability
Flame cutting can handle steel thicknesses from 6mm up to an impressive 270mm, making it ideal for heavy-duty projects and applications.
Cutting Bed Size
Our large cutting beds (42m x 5m) facilitate high production runs on substantial steel plates.
Multi-Head Cutting
Equipped with multi-headed machines, our flame cutting services are highly efficient for large production runs, reducing costs per part.
Material Versatility
Flame cutting works exceptionally well with mild and carbon steels, available in various grades and thicknesses.
Tolerance and Precision
Adhering to BS EN 10029:2010 standards, flame cutting offers thickness tolerance in Class A and profiling tolerance ranging from +/-2.0mm to +/-6.0mm.
Flame Cutting Applications
- Manufacturing and Fabrication
- Construction
- Shipbuilding
- Automotive Industry
- Metal Recycling
- Pipeline Construction and Maintenance
- Railroad Industry
- Aerospace Industry
- Art and Sculpture
- Maintenance and Repair
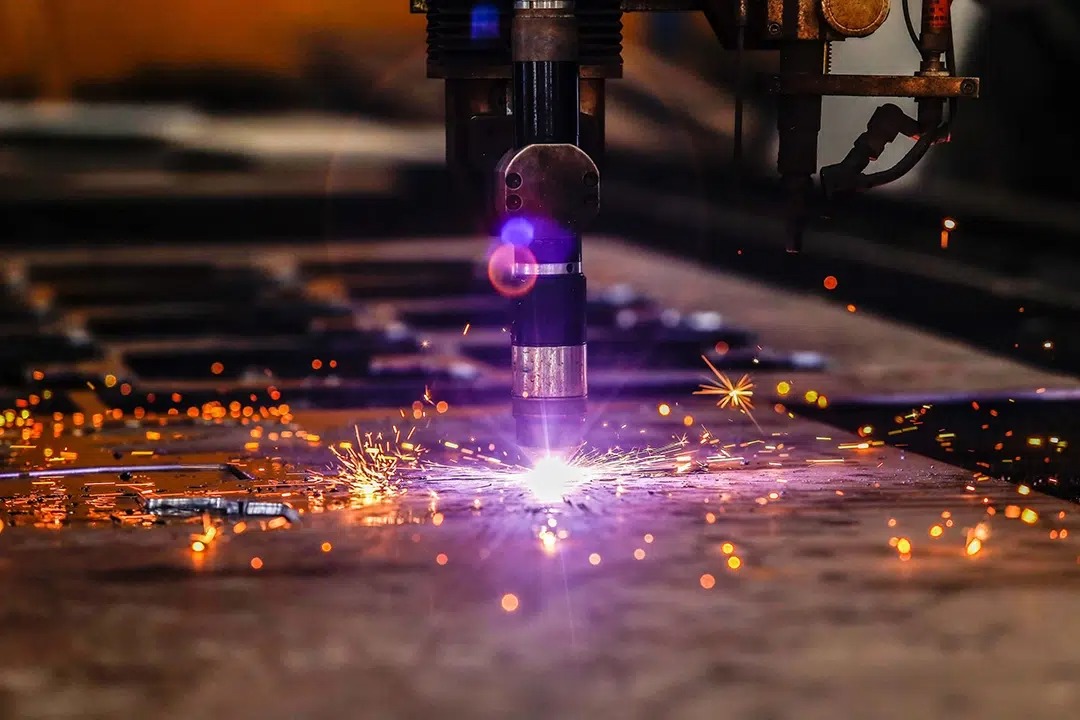
What is Plasma Cutting?
Plasma cutting, uses a jet of ionised gas at temperatures exceeding 20,000°C to melt and expel material from the cut. While plasma cutting has its merits, flame cutting remains a highly effective and versatile solution, particularly for thick steel applications.
Key Features of Plasma Cutting:
Cutting Thickness
Effective for materials up to 30mm thick, with the capability to handle carbon steels up to 40mm thick through edge start cuts.
Material Versatility
Can profile a wide array of materials including stainless steel, carbon/mild steel and aluminium.
Precision and Edge Quality
Delivers smooth cut edges and better edge squareness compared to some other methods.
Speed and Cost Efficiency
On certain thicknesses, plasma cutting can be faster and more cost-effective than flame cutting.
Plasma Cutting Applications
- Manufacturing and Fabrication
- Automotive Industry
- Aerospace Industry
- Construction
- Shipbuilding
- Metal Art and Sculpture
- Metal Recycling
- Maintenance and Repair
- Pipe and Tube Cutting
- Signage and Metalwork
- HVAC Industry
- Job Shops and Prototyping
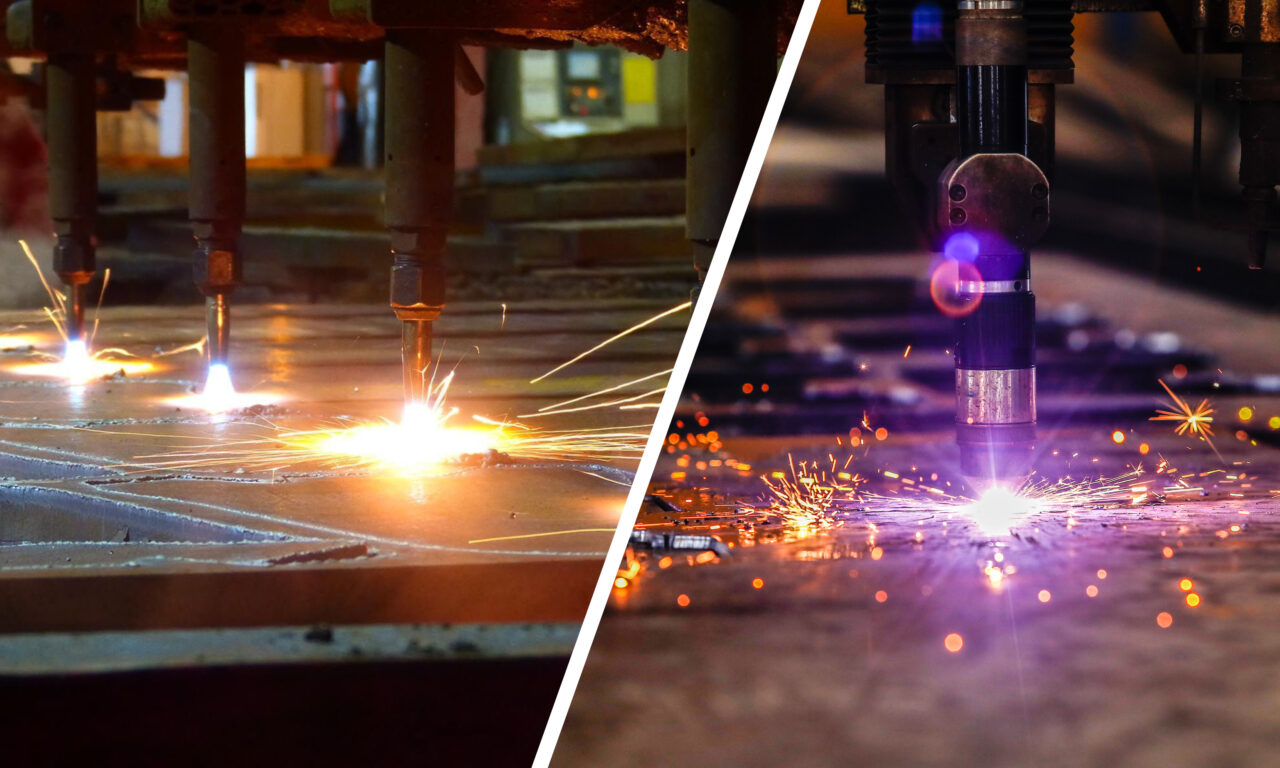
Flame Cutting Vs Plasma Cutting
Flame cutting uses oxygen and fuel gases to create a high-temperature flame for cutting thicker ferrous metals like steel. It’s cost-effective and portable, suitable for construction and industrial applications. Plasma cutting, using ionised gas and an electrical arc, can cut various metals like stainless steel, aluminium and copper.
Comparing Flame Cutting and Plasma Cutting
Material Thickness and Type:
Flame Cutting
Best for thicker materials, especially mild and carbon steels, with thicknesses up to 270mm. Flame cutting is particularly effective for large-scale and heavy-duty projects.
Plasma Cutting
Suitable for a variety of metals including stainless steel and aluminium, effective up to 40mm for carbon steels.
Precision and Edge Quality:
Flame Cutting
Offers excellent precision with potential post-processing to handle HAZ and edge burring, ensuring high-quality results for robust applications.
Plasma Cutting
Provides superior precision with smoother edges but may not handle the same thicknesses as flame cutting.
Cost and Efficiency:
Flame Cutting
More cost-effective for thicker materials and large production runs due to multi-head capabilities, making it a highly economical choice for substantial projects.
Plasma Cutting
Faster and potentially cheaper for certain thicknesses and materials, but less effective for very thick steel.
Production Speed and Lead Time:
Both methods are efficient, but flame cutting is particularly advantageous for large-scale projects due to its capability to handle very thick materials efficiently.
Trust Charles Day Steels for Professional Flame Cutting and Plasma Cutting Services
Choosing between flame cutting and plasma cutting depends largely on your specific project requirements. Flame cutting, with its ability to handle very thick materials and large production runs, remains a cornerstone in heavy-duty steel profiling. Our state-of-the-art laser cutting capabilities further extend our ability to provide precision cutting up to 50mm, offering another versatile and high-quality option.
No matter your requirements, our state-of-the-art profiling capabilities and professional team here at Charles Day Steels ensures high-quality, cost-effective and timely solutions tailored to your needs.