Laser cutting has come a long way since its inception in the 1960’s. 2D and 3D laser cutting are among several names used to reference all that can be achieved with a laser cutting machine. Industrial laser cutting is one part of a value chain always seeking to gain efficiencies and boost margins. Every part of the process, from sourcing raw materials to assembly, holds the potential to work smarter, if you know what your options are.
In this guide, we provide an overview of industrial laser cutting and how manufacturers can derive high value benefits from the technology. While laser cutting is well established within large manufacturing corporations, the cost of investing in the technology is often out of reach for smaller businesses constantly navigating headwinds of the unsteady global economy. Yet there are still ways harness the benefits of the industrial laser cutting.
Introducing Fibre Lasers
Solid state fibre lasers have overtaken their CO ² counterparts in recent years as advances in the technology shift the table of pros and cons in fibre’s favour. Here are 5 reasons why fibre lasers are ahead of pack when it comes to industrial cutting:
1. Fast and Accurate
It was once the case that fibre lasers couldn’t match the ability of CO ² lasers to cut through thick material burr-free. Now that 20kW fibre lasers are making their way into workshops across the UK, this cutting technology is able to take on the demanding jobs with ease. When we say, thick, we mean 50mm cutting depth which caters for the vast majority of heavy-duty cutting jobs.
2. Energy Efficient
One of the many reasons fibre lasers have become so popular is, relatively, low power consumption. Manufacturers are leading the way in sustainable business practices and investing in efficient machinery goes hand in hand with initiatives such as renewable energy use and zero landfill waste. The average fibre laser consumes three to five times less energy than CO ² lasers, have a shorter and less energy-intensive start-up procedure, and generate less heat. As an example, a 2kW fibre laser cutter can process materials at the same rate as a 4 to 5kW CO ² laser.
3. Less Waste
Fibre lasers are accurate enough to reduce waste during cutting by having a shorter wavelength than CO ² lasers, producing highly focused cutting power. As a result, designers can nest sheet metal layouts much tighter with a cutting tolerance of +/- 0.25mm for consistent and reliable precision. CO ² lasers are prone to generating damaging levels of heat that require materials to be further processed after cutting. Fibre lasers produce far less heat and can cut thin sheet metals without causing showstopping substrate deformation.
4. Compact Machinery
Fibre lasers are a compact technology and as such, require less materials for manufacture and maintenance, known as a small industrial footprint. An optical fibre cable transmits a wavelength emitted by the mixing of rare earth elements, such as ytterbium and neodymium, to produce raw laser light which is manipulated into a laser beam. Several elements of the process can be tweaked to meet different applications, such as cutting, engraving, or annealing, and to profile a wide range of materials.
5. Better Service
Metal profiling is a process being increasingly outsourced by manufacturers as a means to keep up with technology. A profiling supplier can take on a large portion of the manufacturing process, using the most accurate and efficient cutting methods available. The return on investing in an industrial laser cutting machine will often be too lengthy for the average manufacturer however, this is the bread and butter of laser profiling shops who will make use of the most accurate and fastest industrial laser cutting machines. Outsourced profilers are able to pass on competitive pricing and rapid lead times to customers.
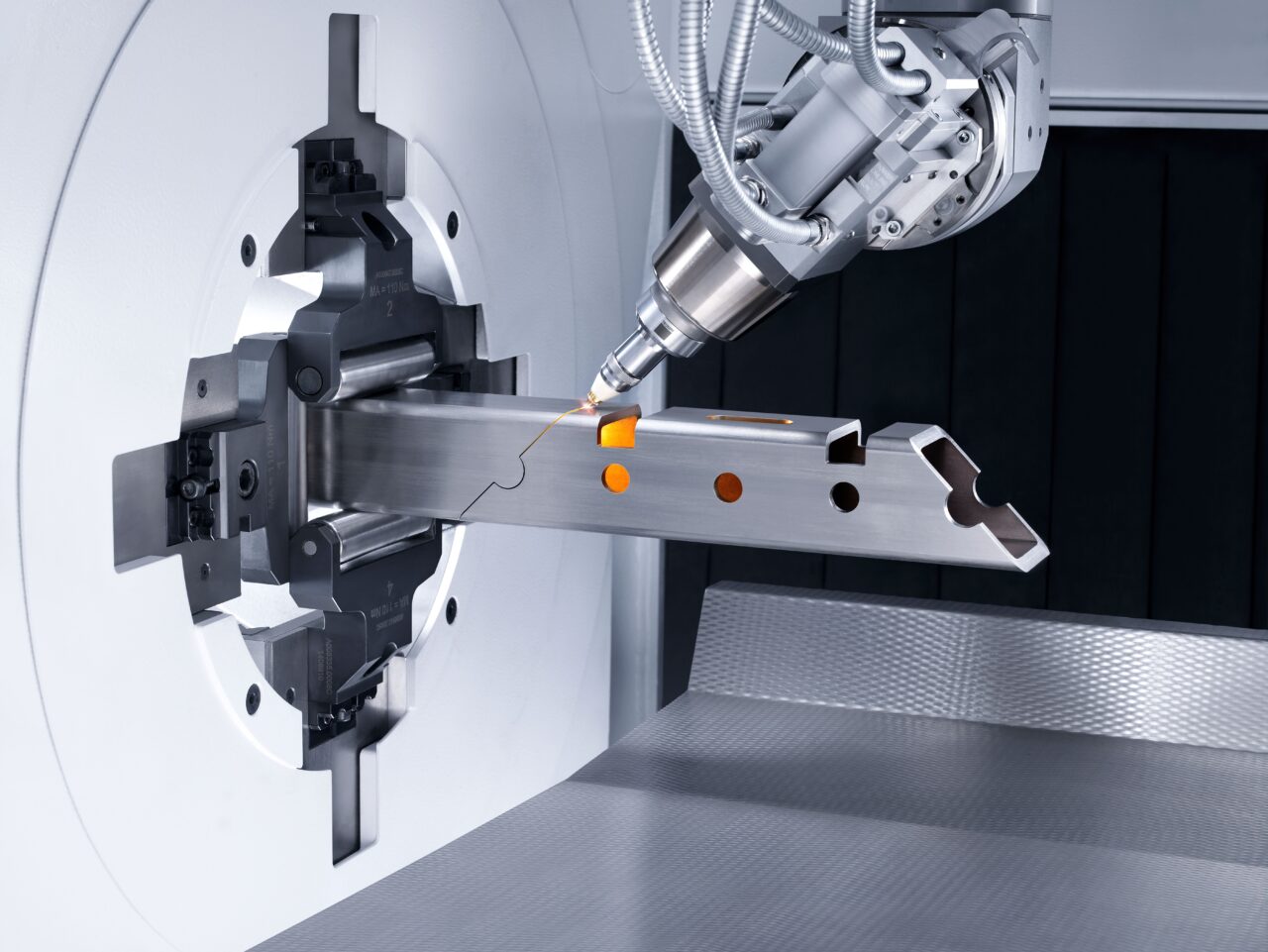
2D or 3D Laser Cutting?
We are often asked what the difference between 2D and 3D cutting is, though these terms seem to be used less in recent years. Customers tend to refer to 2D cutting as sheet metal cutting, and tube cutting or section cutting rather than 3D.
Flatbed or sheet metal cutting machines usually handle standard sheet sizes of 4 metres by 2 metres and 3 metres by 1.5 metres, cutting materials up to 50mm thick. 2D industrial laser cutting can achieve impressively intricate profiling, meaning more parts can be cut from a single sheet with less waste.
Tube laser cutting machines no longer operate solely on 3 axes, X, Y and Z, but they now function on 6 axes, able to tilt and rotate materials for intricate part cutting. The increasing use of structural tubing means 3D industrial laser cutting is a key part of the value chain in construction, machine building, and furniture manufacturing, for example.
Manufacturing for Efficiency
The advent of 3D industrial laser cutting has opened myriad opportunities for manufacturers to reduce materials, weight, processes, and storage requirements for individual product lines. When every design choice has a knock-on effect downstream, the ability to optimise product design can make all the difference to costs, speed, and quality of manufacture.
Tube laser cutting can reduce the volume of parts required for an assembly, replacing welds with part folds, self-jigs, and slots and tags. Assembly is faster, finished products more accurate, and work in progress stock is minimised.
Receive Materials Ready for Assembly
The value of industrial laser cutting today, is that manufacturers can outsource the whole process to a profiling shop and make full use of the latest cutting technologies without having to make eyewatering investments. Outsource your industrial laser cutting to benefit from:
- Aggregated materials purchasing
- State-of-the-art profiling technologies
- Fully weld prepared parts
- Implement Design for Manufacture principles
- Lower cost per part
- Rapid turnaround of high volume and high complexity jobs.
Interested in the benefits of industrial laser cutting? Send us your drawing, production volumes and assembly capabilities, and we will send you a quote or your next project. Charles Day profiling services include:
- Tube and Sheet Laser Cutting (up to 6 metres by 2.5 metres)
- Waterjet cutting
- Flame cutting
- Plasma cutting
- Profile bending and pressing
- Bevels and countersinks
- Shot blasting
- Deburring and Vibra-deburring
- Laser engraving.
Get a no-obligation quote for your next project and see how much you can save: