The use of aluminium has become indispensable across several sectors, most notably within automotive and aerospace industries where there is an essential requirement for lightweight and robust metals. However, aluminium can be a challenging metal to work with due to its specific properties, therefore it requires careful weld preparation and techniques to achieve optimum quality that meets relevant standards.
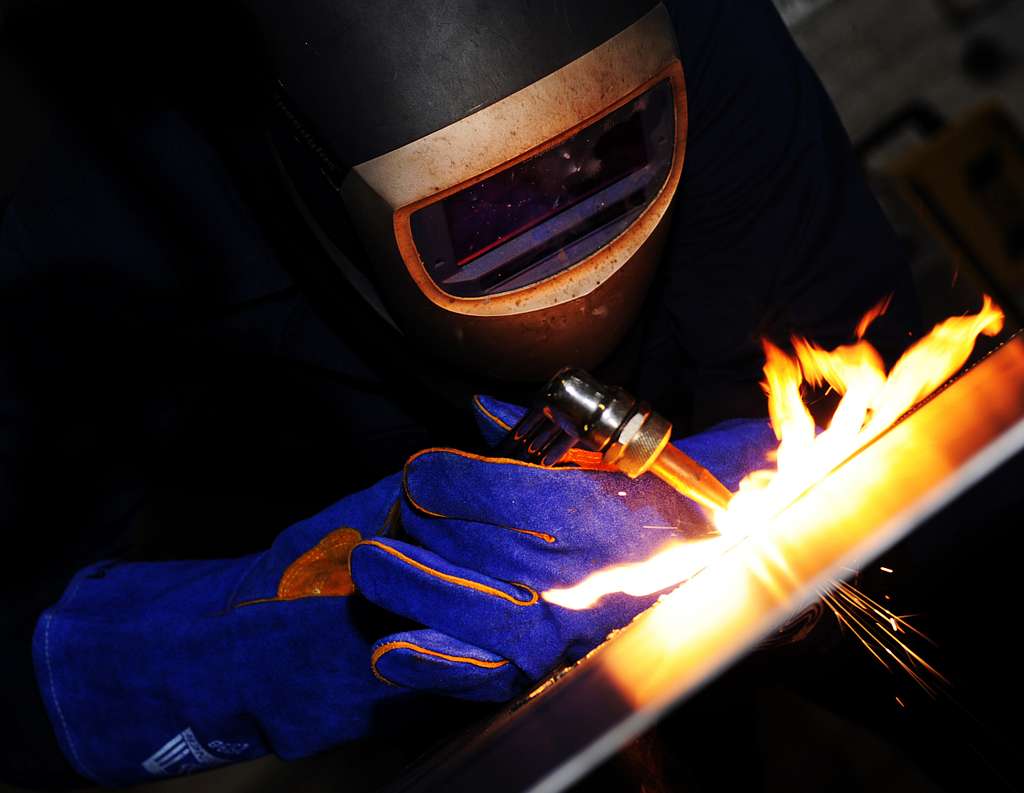
The Difficulties of Welding Aluminium
When aluminium reacts with oxygen, it forms an oxide layer as a protectant against potential corrosion and abrasion. Due to this layer, it can also insulate the metal, proving a challenge during a temperature-controlled welding process. This allows for various difficulties to emerge during welding that affect porosity and thermal conductivity.
Porosity
During the welding process, aluminium becomes a liquid state and absorbs large amounts of hydrogen. This creates issues due to the formation of bubbles within the metal, essentially weakening the integrity of the sheet and creating a final product that is not viable for use.
When welding aluminium, clean equipment must be used from the start and the potential for any debris, grease and oil should be sufficiently removed from the metal. Additionally, a shielding gas is imperative to reduce contamination of the metal.
Oxidisation
The oxide layer that forms across aluminium also functions at a significantly higher melting point of 2,072°C, compared to aluminium at 660°C. Improper welding prior to preparation, in attempts to combat the oxide layer, can cause defects and holes within the metal. Common practice includes utilising abrasive solutions such as an acid or solvent as preparation to tackle any physical impurities.
Hot Cracking
The welding process affects metal types differently, and the low melting point of aluminium puts the metal under substantial thermal stress. This can result in the process of hot cracking to occur. Such circumstances can be mitigated by combining aluminium with an appropriate alloy as a filler material, therefore reducing distortion during the welding process.
Thermal Conductivity
Aluminium dissipates heat from the welding area due to its high thermal conductivity. This results in the weld becoming less efficient as it cannot effectively penetrate the metal. Utilising a higher heat output will allow the weld to reach its desired effect. A thorough understanding of different techniques for sheet thickness and specified parameters is essential to achieve high-quality results.
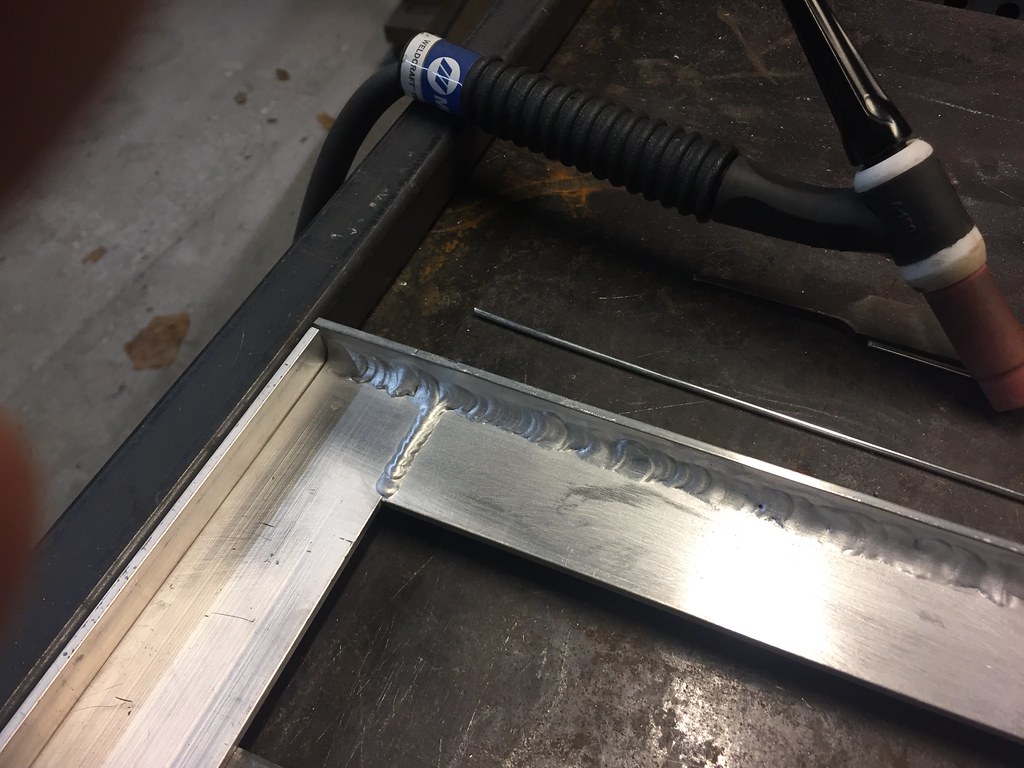
Aluminium Welding Methods
There are several welding methods applicable when working with aluminium, all designed and specially tailored to meet the challenging components of the metal.
GTAW/TIG
Also known as Gas Tungsten Arc Welding or Tungsten Inert Gas Welding, this is the most common method utilised with aluminium. Employing a tungsten electrode, the current, voltage, speed and shielding gas have set parameters based on the weld method and sheet thickness to achieve a specified outcome. Known for its quality precision, this method produces clean results as it eliminates impurities and clears the metal from its oxide layer.
A filler metal is fed into the puddle by hand, increasing the capacity to weld varying sizes of aluminium, whilst protecting the metal with inert gas to combat oxidation.
GMAW/MIG
Ideal for thicker sheets of aluminium, Gas Metal Arc Welding works similarly to TIG welding but with an electric arc instead of a tungsten electrode to establish strong metal fusion. With a higher heat input compared to TIG, GMAW typically has a higher deposition rate and faster travel speeds. Due to this method being wire fed, a dedicated spool gun is utilised and shielding gas is standard to protect against contamination.
Laser Beam and Electron Beam Welding
A popular choice for welding, laser beam offers precise accuracy across varying material depths that can weld aluminium due to its highly focused beam that fuses a connection. Hot cracking is a real concern due to the high heat input, therefore a filler metal is often used to achieve optimal results. Laser beam welding provides clean finishes with very little to zero post-processing.
Electron beam welding delivers controllable and precise results, which makes it a top contender among welding processes. The method first involves chemically cleaning the metal to remove the oxide layer, the electron beam then performs in a vacuum environment that effectively eliminates impurities. With a deep but narrow heat affected zone, the electron beam is excellent at mitigating distortion and cracking of the aluminium.
Resistance Welding
This process commonly uses spot welding which utilises pressure to combine metals. This method must consider the specific parameters for the particular welding outcome due to the thermal conductivity of aluminium and the use of a high power welding gun.
Processes that use flux within the filler metal are advised against, this is due to the material’s increased risk of porosity during the welding process.

Weld Prep and Chamfer Services
Weld preparation of metal parts from a dedicated supplier saves valuable time and money, with a combined cutting and beveling process that effectively reduces steps across the supply chain. The benefit of weld preps is that the metal surface is processed to ensure excellent weld strength, with the service including cleaning, cutting, fitting, and beveling. This ensures that the surface is efficiently prepared to apply filler material and varying heat inputs. Weld preps and chamfers are often provided in angles up to 60 degrees and on plates between 6mm to 60mm, all within rapid lead times.
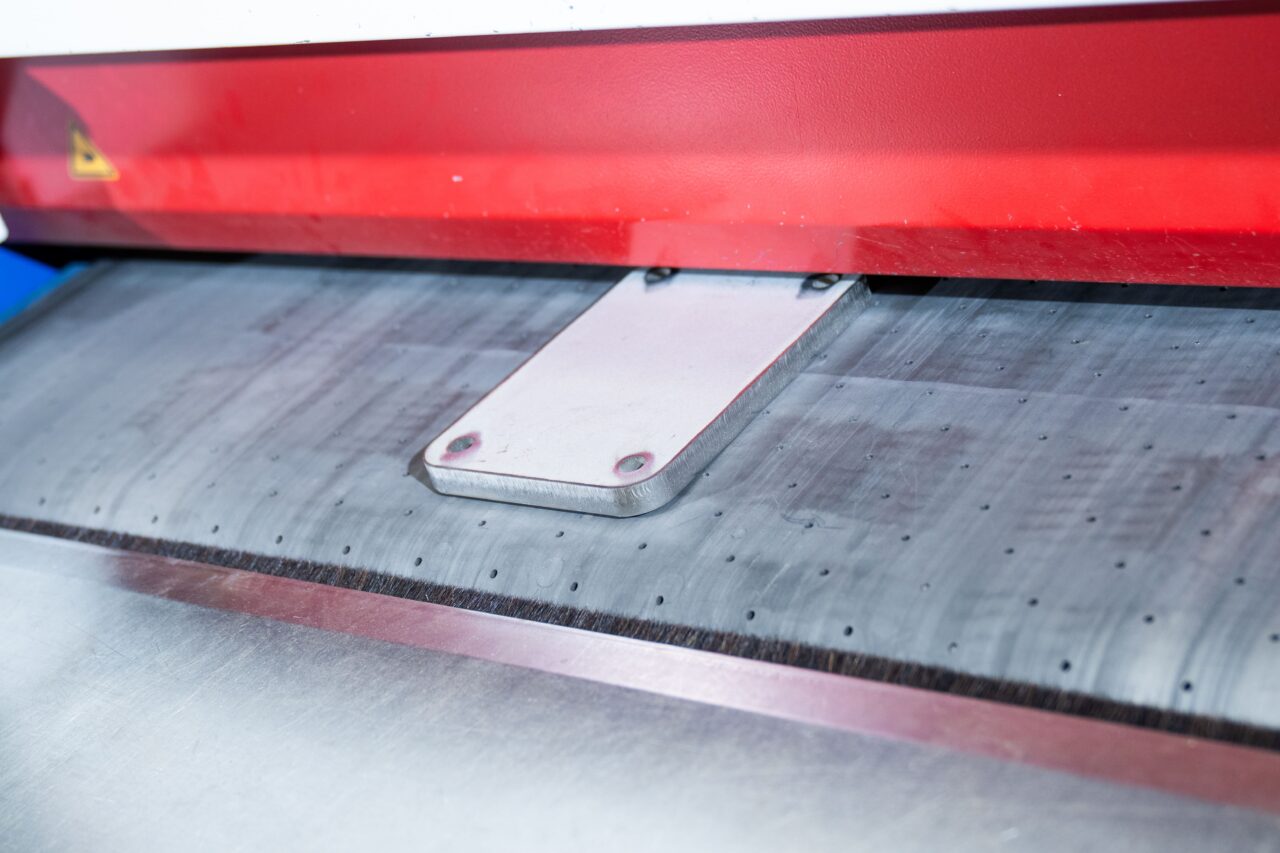
Trust Charles Day Steels for Exceptional Weld Prep Solutions
Establishing efficient preparation before welding is fundamental to achieving high-quality results. With a suite of high-spec and innovative machinery on site, Charles Day Steels has the technical expertise and experience to handle complex projects and bespoke metal profiling services.
Our engineers can produce top-face, bottom-face, or a combination for edge preps between 15° – 60° on varying metal depths, with greater thicknesses available on request. With a team of CAD experts, support is provided from the early design stage, ensuring your weld preps, chamfers and bevels are procured in a timely manner.
At Charles Day, we strive to provide the very best in metal profiling and continuously invest in the most innovative software that streamlines processes for our clientele. Capable of processing a plethora of weld joint configurations, chamfers, and bevels, we work closely with you to achieve the highest quality possible. Get in touch with a member of our team today to discuss your weld prep and chamfer requirements.